The Liebherr Autonomous Operations system is designed to enhance efficiency and safety in the use of wheel loaders. It allows repetitive and monotonous tasks to be carried out easily and intuitively without an operator.
According to Liebherr, the system is currently at an advanced stage of development. It recently won the bauma 2025 Innovation Award in the ‘Digitalisation’ category, which was presented at the ICM in Munich on the eve of the opening of bauma on 6 April.
Developed by Liebherr-Werk Bischofshofen GmbH, based in Austria, this autonomous system is ideal for activities such as repeatedly loading hoppers or transporting materials from A to B without an operator. As a result, employees can devote themselves to more varied tasks, so that working time can be organised more effectively.
“At the same time, it can create space for employees to focus on more complex activities that require human expertise,” said Dr Manuel Bös, head of emerging technologies at Liebherr-Werk Bischofshofen. Challenging tasks such as working in the hazardous area of a quarry can also be performed by the autonomous system, boosting jobsite safety.
Operators can plan deployments of the autonomous wheel loader using the Autonomous Job Planner web application developed by Liebherr. “You don’t need any special IT skills to initiate the wheel loader deployment. The system is very intuitive and user-friendly, and requires only a few inputs for the job,” explained Mr Bös. The machine perceives its surroundings, piles and obstacles using 3D environmental sensors – without having to use drones or separate surveying technology – and plans the work cycle accordingly.
The autonomous system then carries out the task independently, automatically adapts to the changing environment and does not require GPS reception, which means it can be used indoors, underground, at high quarry faces or under tree cover. “In these operations, conventional GPS-based systems reach their limits, while Liebherr Autonomous Operations can be used anywhere – from a confined industrial hall to an open quarry,” highlighted Mr Bös. The self-driving wheel loader can also operate independently around the clock, enabling continuous material handling at any time.
Furthermore, the autonomous system delivers machine operation with consistent performance and efficiency right from the start and throughout the entire duration of use, regardless of the time of day. “Due to the consistent performance of the autonomous wheel loader, all processes are easier to plan and can be made more efficient,” added Mr Bös.
“The software-controlled autonomous wheel loader operates in a particularly machine-friendly way, significantly reducing component and tyre wear as well as fuel consumption. This reduces ongoing operating costs,” he pointed out. “Additionally, the operator can seamlessly switch between conventional manual cab operation and fully autonomous operation, thus maximising machine utilisation.”
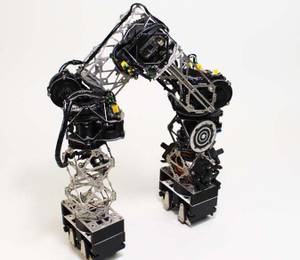
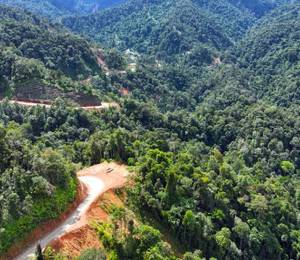
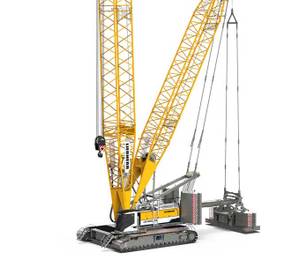
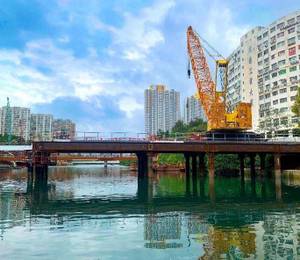
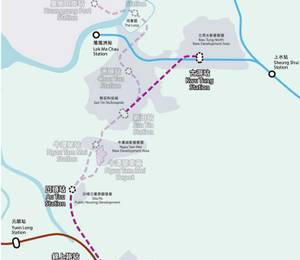
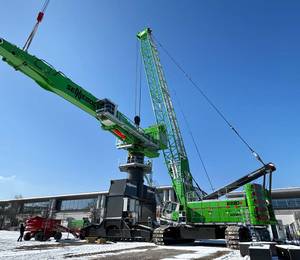
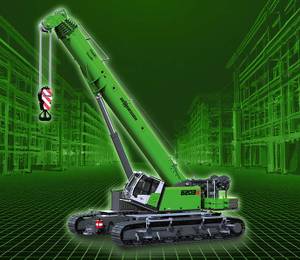
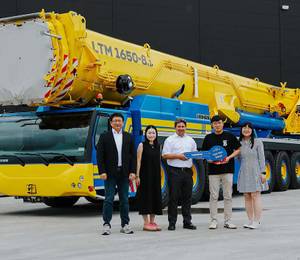