In 2022, the Housing and Development Board (HDB) – Singapore’s public housing authority and a statutory board under the Ministry of National Development – launched the Construction Transformation Project (CTP) to kick-start the next phase of HDB’s productivity transformation journey towards its 2030 target, adopting various advanced technologies in the design and construction of its BTO (build-to-order) projects, Garden Waterfront I & II @ Tengah. The CTP, which is a partnership with construction firm Obayashi Singapore Pte Ltd, aims to realise a 25% improvement in site productivity, compared to other BTO projects.
The innovative technologies tested in Garden Waterfront I & II @ Tengah are expected to yield higher productivity through more efficient use of manpower and resources. These innovations, including those below, will be studied for possible wider-scale implementation in future BTO developments.
AI in autonomous tower crane
To enhance the efficiency, safety and precision of tower crane operations, AI is being used in the autonomous tower crane integrated with Skyjuster. AI helps to automate the lifting and transportation of precast components, and adjust the orientation of the suspended components mid-air for greater precision, which speeds up installation of precast components. This will enable HDB to build flats faster and safely, compared to traditional construction methods.
Before any on-site works begin, a comprehensive virtual design and construction model using building information modelling (BIM) is developed and seamlessly integrated with the autonomous tower crane. This information model (digital twin) specifies the placement of each precast component, before they are hoisted. The digital twin is continuously updated during the installation process to help the crane monitor live construction activity and maintain the required safety clearance from installed structures.
To initiate hoisting works, the operator only needs to touch a button in the cabin, then the crane autonomously lifts and transports precast units through the shortest safe route to their designated locations recorded in the BIM. This streamlined process reduces operator fatigue and enhances operational efficiency on-site.
During the automated hoisting and placement, the crane operator also acts as a safety contingency, where they can manually override the movement of the tower crane should they notice any potential safety hazard.
The integration of the Skyjuster – which houses a gyroscope – to the lifting frame further enhances the crane system by eliminating swaying motions of the modules, and automating the rotation and positioning of suspended components to the intended alignment before they are lowered into place. It removes the need for manpower to provide manual rope guidance, and speeds up the construction process while enhancing overall safety, especially for large and heavy precast modules that require significant effort to manoeuvre.
The entire installation process from hoisting to final placement is monitored live through the digital twin model remotely at the site office, ensuring accurate and safe installation.
Crane machine guidance
Another innovation being piloted as part of CTP is the crane machine guidance technology, which is being used in mobile cranes for the construction of a multi-storey car park. The technology incorporates advanced safety features, thereby enabling two adjacent mobile cranes to operate safely and simultaneously within a confined space, with less manpower.
The GPS system on the mobile cranes defines each crane’s specific operational zones to ensure their safe movement, and the sensors on the crane’s boom provide alerts to the crane operator to ensure that safe distances between the cranes are maintained. Light Detection and Ranging (LiDAR) sensors on the boom also provide the crane operator with feedback on the vertical accuracy of the hoisted components and detect potential obstructions in the object’s path, therefore facilitating precise and safe component installation without the need for an onsite spotter.
In addition, the crane machine guidance technology provides mobile crane operators with a birds’ eye view of the construction area, eliminating the need for traditional walkie-talkie communication with workers to manoeuvre the boom, and enabling tasks to be carried out safely and with greater precision, in a shorter time.
All images: HDB

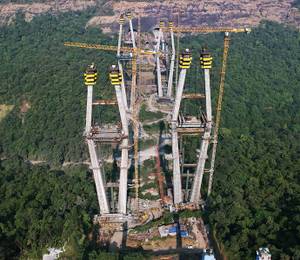
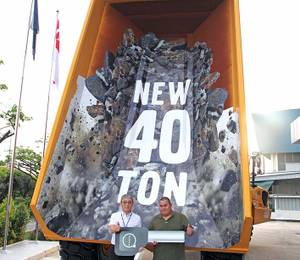
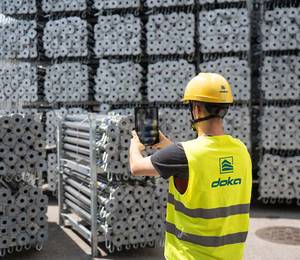
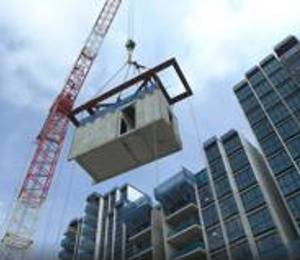
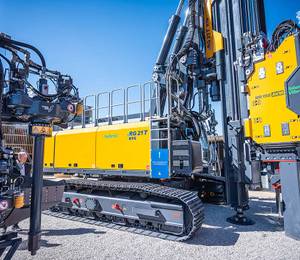
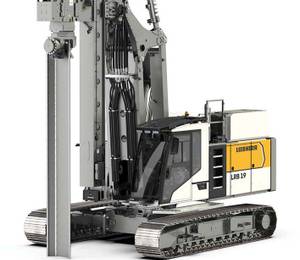