Surbana Jurong’s new global headquarters is one of the latest engineering feats in Singapore. It features various innovative designs and was built using advanced construction technologies.
Surbana Jurong (SJ) recently opened its new global headquarters, which is located within CleanTech Park in Jurong Innovation District (JID), Singapore. Covering a built-up area of 1,200,000 sq ft, it can accommodate up to 4,000 onsite employees and the wider community.
For the first time since SJ’s formation as a collective of built environment consultants in 2015, employees from different entities in Singapore finally congregate under one roof. The new campus has been designed with both the SJ community and the community-at-large in mind.
The campus serves as an incubator for real-world urban solutions to demonstrate the scalability of emerging technologies to the built environment industry. SJ is currently working with Singapore’s Building and Construction Authority (BCA) to test-bed low-carbon technologies to save energy and improve occupant health.
Dubbed ‘Campus in Nature’, the new SJ Campus was designed by Safdie Architects working with SJ’s architects. The civil and structural engineer for the project was KTP Consultants (a member of SJ), while the main contractor was Boustead Projects.
SJ’s multidisciplinary team undertook much of the work that brought the campus to life, providing consultancy services from architecture, landscape architecture, engineering and project management, to workplace strategy, integrated facilities management and security services.
Situated on a previously undeveloped greenfield site, the SJ Campus design preserves more than half of the site’s existing green space and replaces built-upon green areas with rooftop gardens, lush interior gardens and extensive exterior landscaping. At the outset, a detailed mapping and analysis of the site was performed to plot the specific location of the existing flora, including a Banyan tree estimated to be over 60 years old.
The 10 towers of the campus are linked by a pedestrian spine and enclosed courtyards, which allow for natural light and fresh air. Other facilities include a 1,000-seat multipurpose area, a junior ballroom, rooftop terraces, a team lounge, table tennis, and soon to be opened, a gym.
A showcase of engineering marvels
SJ Campus was constructed in three phases: Phase 1 was completed in October 2022, Phase 2 in April 2023, and Phase 3 in May 2023. A ceremony was held on 13 March 2024 to mark the official opening of the campus.
It is one of the first large-scale, non-residential buildings in Singapore to fully adopt the integrated digital delivery (IDD), which involved a ‘digital spine’ linking project stakeholders throughout the building lifecycle. This resulted in a 12% improvement in overall productivity.
The design for manufacturing and assembly (DfMA) technology was also applied during construction, with the campus being one of the first projects in Singapore to fully adopt prefabricated mechanical engineering and plumbing (prefab MEP). The use of prefab chilled water system pump and ducting system generated about 6% reduction in manpower/man-days compared to the conventional MEP method.
Discussing the engineering highlights of SJ Campus, Aaron Foong, qualified person (structure) for the project and managing director of KTP Consultants, shared, “What is very unique about the structural framing is that we are able to use repetition in the concrete element sizes, the beams and the columns to create the geometry that is so different.”
“It is one of our most challenging projects,” he said. “If you look at the way that the building blocks are laid out, the engineers have actually applied productive technologies and there is a certain interaction between all the various elements that come together.”
The main entrance is a key engineering complexity in SJ Campus. It features a large glass canopy, up to 16 m in length (with a span-depth ratio of 1:40), without any support of conventional tiebacks, thus requiring sophisticated parametric analysis.
“This ultra-slim canopy is different from the typical roof structures that use either tieback cables or columns,” explained Mr Foong. “The three-dimensional profiling of it enables us to come up with this sort of functional engineering artwork.”
Having no tiebacks or columns means there is more space on the ground, Mr Foong pointed out. “It is also more appealing aesthetically, creating a grand statement at the entrance.”
He added that the installation of the whole canopy, which took about two months, had to be performed “meticulously, stage by stage, to ensure that the curvature of the structure would not cause the glass to break.”
At Tower 1, the A-frame structure stabilises both sides of the campus by acting as the ‘spine’ to withstand any movements of the buildings. It also gives the building a unique spatial quality and allows a column-free space for the spine.
To navigate the challenge of high heat and glare from the tall glass windows at the spine, a careful and strategic performance-based simulation was conducted to optimise the building massing which considers the windows on each side of the campus, the treatment and material of glass, and other shading optimisation strategies. The result is picturesque green views with less heat and glare, and overall thermal comfort.
SJ Campus’ inverted pyramids – the stacks of cantilevered blocks resembling an ‘upside-down’ building – were constructed using the DfMA technology. These structures form self-shading terraces, reducing solar radiation by a significant 36%.
Built with precast concrete beams and columns, it reduced the time and resources needed, compared to conventional on-site construction. To minimise carbon emissions from the transportation of the precast materials, beams and columns were cast on a site adjacent to the campus.
“Additionally, we applied the post-tension technology to these inverted pyramids in order to prevent the long-term deformation posed by such geometry,” said Mr Foong.
What truly keeps the campus ‘stitched’ together is the central spine, which is long, curved and supported by trusses, columns, arches and tie beams.
“The central spine is made up of a series of A-frame steel spine, which caters to the movement between the eastern block and the western block,” Mr Foong further explained. “It gives that sense of space, as the shape itself opens up the entire thoroughfare for people to walk through, to enjoy the surroundings around them.”
The intricate integration of the 10 tower blocks into the slender central spine – comprising multiple steel, concrete, glass and ethylene tetrafluoroethylene (ETFE) – features complex structural engineering analysis, design, detailing and construction.
Another highlight of SJ Campus is a multi-storey hanging block that expands the space for use. “It is a very clever way to use airspace because you’ll have a lot of usable space below it,” said Mr Foong. “With an innovatively positioned warren truss at the top, it hangs three storeys of usable office space, without having any footprint on the ground. This enables the entire atrium space to grow even larger.”
On the whole, this project is “very unique, as you’re looking at a symphony of sorts,” described Mr Foong. “Unlike in typical engineering applications, where most elements are straight.” For SJ Campus, it is an “ensemble of all different engineering elements that must come together and yet be stable.”
Having overcome so many challenges to successfully deliver such an iconic landmark, Mr Foong said, “The greatest satisfaction from the perspective of an engineer is the validation of our design. Both the public and the private can really enjoy the outcome of innovative engineering and a product that is sustainable, highly productive and highly liveable.”
‘Green’ campus
SJ Campus has adopted one of the largest underfloor air distribution systems in Singapore. This provides efficient cooling from below to target occupied space and improve indoor air quality and additional energy savings of up to 16% of the cooling energy required. Other smart facilities management solutions include an Integrated Command Centre, where IOT devices leverage artificial intelligence and machine learning to monitor energy, water, occupancy patterns and indoor air quality to optimise carbon management and improve productivity. These active systems and natural design elements work in combination to achieve an overall energy saving of 41%. The campus is estimated to save 4.4 mil kWh/year operational energy savings, which is equal to avoiding 1,785 t of carbon dioxide per year, based on Energy Market Authority’s grid emission factor.
SJ Campus has also integrated a next-generation solar photovoltaic (PV) system using bifacial PV panels, which can produce clean energy when illuminated on either of its surfaces. The solar rooftops serve as a test-bed for advanced PV technologies, energy storage and the deployment of a smart grid. Located in four towers, it has a combined energy yield of 389 MWh per year, which is equivalent to powering 120 three-room HDB flats every year. On-site renewable energy helps to offset Scope 2 emissions, saves energy costs and earns renewable energy certificates (RECs).
The project was awarded the BCA Green Mark Platinum Super Low Energy (SLE) and BCA-HPB Green Mark Platinum for Healthier Workplaces certification. The campus is designed for maintainability and deploys integrated facilities management to optimise operational efficiency. It is also WELL pre-certified by the International WELL Building Institute for having demonstrated a commitment to incorporate health and well-being features and practices.
Images 1-4: Surbana Jurong
Image 5: Tim Hursley
Note: This story has also been published in the May/June 2024 issue of SEAC (with more images). Click here to read online or here to download the PDF file (pages 50-53).

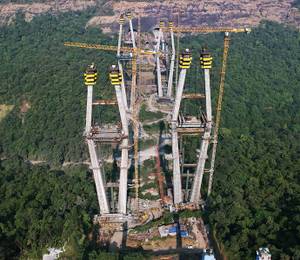
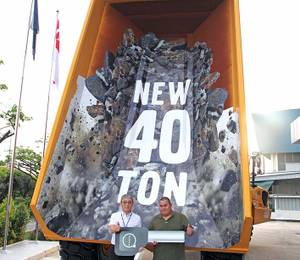
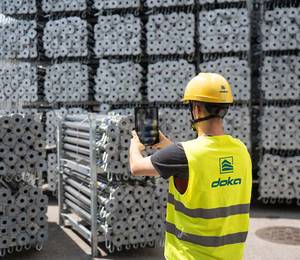
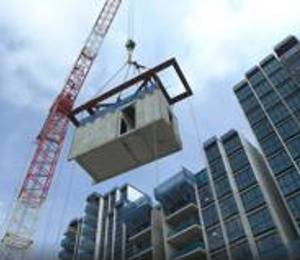
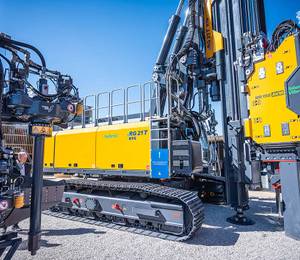
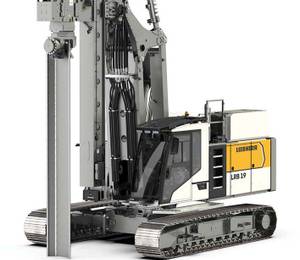