The new Betomix and Mobilmix concrete mixing plant series from Liebherr can be built entirely using a modular system. Customers benefit from a greater range of configuration options, shorter lead times, faster assembly and high parts availability. In addition, these plants are more environment-friendly.
According to Liebherr, the new generation of plants requires up to 30% less energy than the previous versions, and the necessary electricity supply can also be reduced. This is achieved by frequency converters for the drives on the mixer and skip; power peaks can be avoided. Wear on mechanical parts is considerably reduced due to smooth starting and stopping processes for the drives.
Furthermore, thanks to the frequency converter, the speed of the twin-shaft mixer can be changed during the mixing process and adapted to the recipe. The lower energy requirement over the entire service life of the mixing plant constitutes an enormous contribution to environmental protection.
The biggest factor in improving environmental protection is the cement, revealed Liebherr. The frequency converters enable an accuracy of +/- 0.5% when metering cement. With a typical recipe featuring 300 kg of cement per cubic metre of concrete, up to 7.5 kg of cement can be saved. For example, with an annual output of 50,000 cu m of concrete, this corresponds to savings of 375 t of cement per year. Cement production has a global warming potential of 587 kg per tonne. According to this calculation, the new generation of mixing plants from Liebherr can save up to 220 t of CO2 per year.
Electric concrete truck mixers
Liebherr’s ETM truck mixer series with electric drum drive allows concrete to be unloaded at the construction site with zero local emissions. Customers can choose from a number of different concepts: the hybrid version on a chassis with a conventional diesel drive, the fully electric version, or as a semitrailer with any tractor unit.
For the hybrid version, the ETM concrete truck mixers can be combined with a conventional diesel chassis. This means the journey to and from the jobsite is made with a diesel engine. On site, a battery-powered rotating drum is used for mixing, unloading and waiting periods. The battery is charged during the outward and return journey using a smart charging system.
On average delivery trips, it is not necessary to charge the vehicle at a charging station, said Liebherr. Compared to conventional concrete mixers, it is possible to reduce fuel consumption by up to 30% with the ETM series, thereby cutting CO2 emissions by 30% as well. Noise levels are also much lower.
When the ETM truck mixer series is mounted on a fully electric chassis, the electric drum drive is powered by the chassis traction battery. The semitrailer also has an electric drum drive, available again in hybrid or fully electric versions, depending on the tractor unit. A combination involving a gas tractor unit has also been realised.

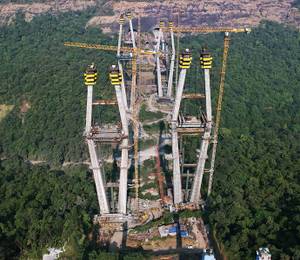
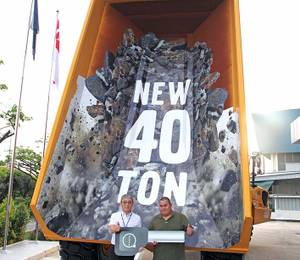
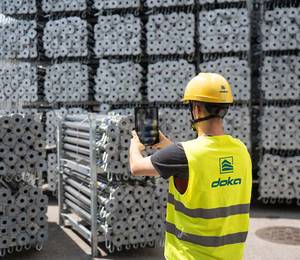
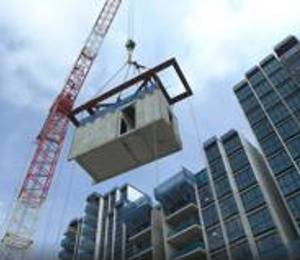
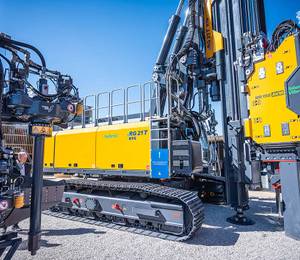
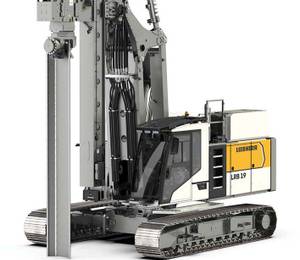