The new Enerpac EMV-series E-mover battery powered load skate is a self-propelled skate featuring a central load bearing plate. It is designed to be used in conjunction with the Enerpac MLS-series wheeled load skates.
The E-mover on show at bauma will include a hydraulic lifting cylinder in place of a load bearing plate and has a 50-t load capacity split between the E-mover and wheeled load skate. The self-propelled skate and lifting cylinder are operated by a wireless remote control. Battery life for the E-mover is expected to be between 3 and 5 hours dependent on usage.
Enerpac will also introduce its new SBL60 telescopic hydraulic gantry, along with the company’s entry-level gantry system for industrial movers, the ML40 Mini Lift Gantry.
The SBL600 Super Boom Lift hydraulic gantry is a three-stage telescopic hydraulic cylinder with rectangular boom for increased capacity and first stage lifting capacity of 674 t and 416 t at the third stage.
The SBL600 lifting height of 10.6 m is ideal for placing gas turbine generators and power transformers in power plants, for example. It is a good fit between the SBL500 and SBL900 gantries with lifting heights of 8.6 m and 11.3 m respectively.
“Ease of transportation is another key benefit of the new gantry. Foldable boom allows for shipping on standard flatbed trucks without special permitting and routing. In addition, with the self-weight less than 9,100 kg, the SBL600 allows for transport of two legs on a single road truck trailer,” said Jeremy Stubbs, commercial director, Enerpac Heavy Lifting Technology.
Accurate synchronised heavy lifting is the hallmark of Enerpac heavy lifting systems. This is well demonstrated by SCJ-series Cube Jacks and their larger JS-series Jack-Up.
The Enerpac Cube Jack has set the standard for ease-of-use and productivity for compact, portable lifting solutions. It uses a base lifting frame and self-aligning, lightweight steel cribbing blocks, together with automatic incremental locking, to provide high-capacity and stabilised lifting. It is a safer, controlled, more efficient and environment-friendly alternative to climbing jacks with tropical hardwood cribbing.
The Enerpac JS-series Jack-Up systems have transformed the way many heavy lift projects are executed. The Jack-Up system is a synchronised lifting and lowering system with self-contained hydraulics in each unit for uncluttered work areas. Loads are lifted in increments as steel boxes (called ‘barrels’) are stacked together to form lifting towers to mechanically hold the load.
The JS-250 Jack-Up system uses computer controls for seamless synchronous control, raising and lowering all towers at the same time. Capacities of the JS-series Jack-Up range from the JS-125, 125 t (500-t lift with four towers) to JS-750, 750 t (3,000-t lift with four towers) with lifting heights from 6 m to 20 m respectively.
Furthermore, electric trolleys like the Enerpac ETR provide distinct advantages over traditional methods of transport, such as skidding systems. When it comes to speed, the ETR can travel as fast as 50 m/hour when loaded. To help tackle large structures, the ETR has a capacity of 500 kN per trolley. They also offer continuous movement, power via a self-contained electric drive, wireless radio control. When used in combination with the SCJ-series Cube Jack and JS-series Jack-Up, they provide greater flexibility for moving heavy loads.
Enerpac strand jacks pack tremendous lifting capacity into a small footprint. They act like a linear winch. A bundle of steel cables or strands are guided through a hydraulic cylinder; above and below the cylinder are anchor systems with wedges that grip the strand bundle. By stroking the cylinder in and out while the grips are engaged in the anchors, a lifting or lowering movement is achieved. The motion of the cylinders is driven by hydraulic power packs. The Enerpac SCC software programme synchronises the motion of the strand jacks and adjusts the motion to the loads per lifting point.
An Enerpac EVO multipoint synchronised lifting system is used to simultaneously control up to 12 cylinders creating a highly accurate and synchronised lift. Operated using a PLC (programmable logic controller), hydraulic cylinders connected to an EVO Synchronous Lifting Pump enable each lifting points to be monitored and controlled by a single operator. The EVO pump maintains accurate positional control within 1 mm between lagging and leading cylinders and includes built-in warning and stop alarms for optimum safety.
Bauma booth: FS.1105/1

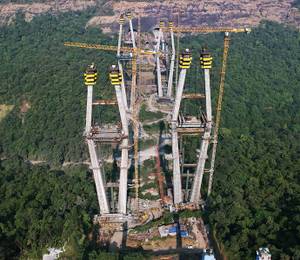
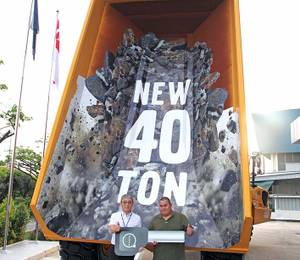
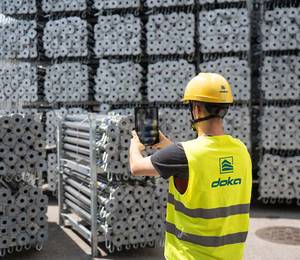
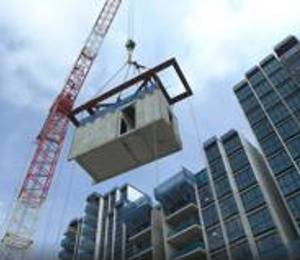
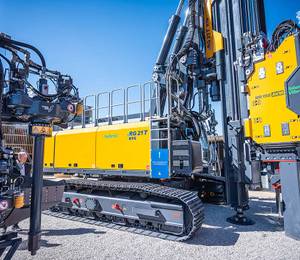
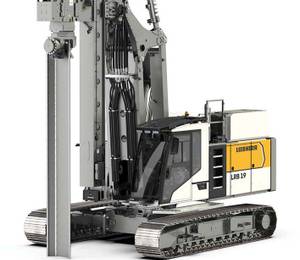