With the new W 100 HR, Wirtgen offers a 1-m-class cold milling machine for cost-efficient operations. Suitable for use on tight jobsites, this model is available to customers in Latin America, Asia Pacific and Russia.
Both the Wirtgen W 100 HR and W 130 HR models are powered by a fuel-efficient engine with a rated output of 155 kW. It drives a newly developed milling drum with HT22 toolholders at any one of three pre-selectable milling drum speeds.
The two small milling machines have excellent manoeuvrability. Their all-wheel drive systems with selectable hydraulic flow dividers ensure consistently high traction and gradeability in all situations. With a speed of 8 km/hr, the machines can be easily relocated and positioned on the jobsite.
The W 100 HR and W 130 HR are designed to deliver high daily production rates with the greatest possible efficiency. Featuring a width of 400 mm, the high-performance belt conveyor carries large volumes of material to transport vehicles at a rate of up to 92 cu m/hr. The conveyor can be slewed by 25° to either side with the joystick of the machine’s intuitive operating concept.
Automatic functions such as a load limitation regulator or a storage function for saving milling depth settings increase productivity, reduce the operator’s workload with standardised workflows, and make daily work much easier.
Three milling drum speeds
Depending on the requirements and on-site conditions, the milling drum of the W 100 HR can be set to mill at three different speeds. Simply by pressing a button, the engine speed can be automatically regulated to deliver milling drum speeds of 1,800 rpm, 2,000 rpm, or 2,200 rpm.
Setting 1 should be selected for low diesel fuel consumption and reduced pick wear; setting 2 enables maximum milling performance in all situations; and setting 3 should be chosen when surface quality requirements are particularly high.
Developed by Wirtgen specifically for cold milling machines, the Level Pro Plus levelling system is also available as an option for the W 100 HR. Fully integrated into the machine control system, this levelling system assures consistently precise milling depths. The high degree of automation reduces the operator’s workload and enables faster milling processes with high quality.
Intelligent operating concept
During milling, the machine is controlled with the control elements integrated in the adjustable armrest of the operator’s seat. These allow, for example, hydraulic height adjustment at two different speeds. The controls for numerous essential machine functions are integrated in the ergonomically-designed, intuitively operable joystick and are therefore always at the operator’s fingertips when needed.
There is also a multifunctional display that supports multiple languages and gives the operator a good overview of all process-relevant data, for instance with a digital milling depth indicator.
An additional option available for the machine is a camera system comprising a camera for mounting at the end of the discharge conveyor and a high-resolution monitor. This allows the operator to view the truck bed of the transport vehicle without having to turn aside from the machine’s direction of travel to look. As such, it increases safety, comfort and efficiency.

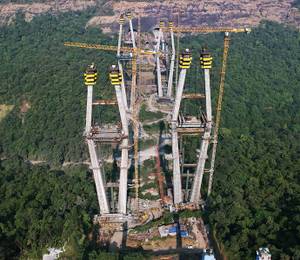
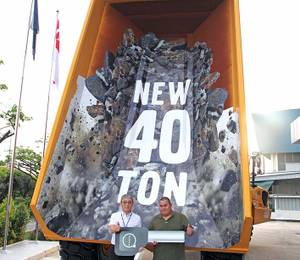
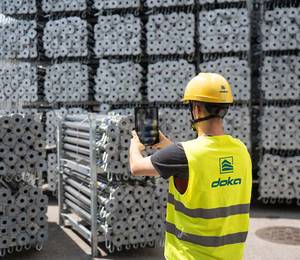
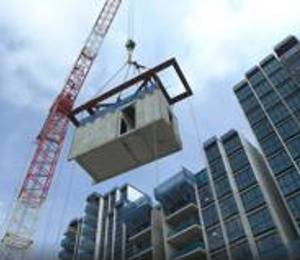
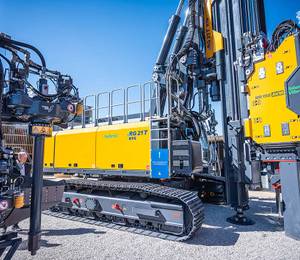
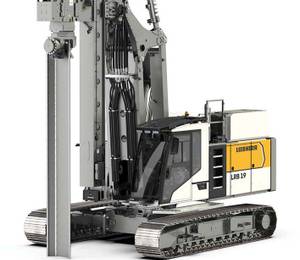