Vermeer expands its lineup of drills for infrastructure development with the new D130S and D60S horizontal directional drills (HDDs) designed exclusively for emerging markets. These machines will be available in select nations throughout Latin America, Middle East and Africa, Asia Pacific and select countries in Europe.
“We understand that operators in Asia, Latin America and other developing nations are looking for a drill that’s specifically for their market,” said Colm Rafferty, vice president of developing markets at Vermeer. “That’s why we designed the D130S and D60S with the power and productivity they have; so that operators in these areas could have drills that meets their needs.”
The new HDD models are manufactured at the Vermeer manufacturing facility in Tianjin, China, and built with “the same high-quality parts and components that Vermeer is known for around the world,” said the manufacturer. The new naming structure indicates a new generation of the pipeline drills from Vermeer for the emerging markets, which comes with several enhanced features that enable high functionality, productivity, and ease of use.
According to Vermeer, the need for the D130S and D60S came from hearing that operators in developing nations needed a way to facilitate greater connectivity and support the development of both rural and urban areas.
“With new infrastructure needing to be developed, including telecommunications (fibre optics), water, electricity, gas and oil pipeline installations across varying ground conditions and locations, a new machine was necessary to take on challenging, large diameter drilling projects without worrying about space restrictions,” explained the manufacturer.
“Both drills are capable of tackling those infrastructure projects. They are also designed to keep surface disruption to a minimum, which helps in densely populated or residential areas.”
“We wanted to create machines that built upon their predecessors, still delivered the same high manufacturing quality and were specific to operators drilling in developing nations,” added Mr Rafferty. “These drills are compact, powerful, and productive enough to appeal to operators large and small, and I believe can make a big difference in a company’s drilling capabilities and efficiencies.”
The D130S is equipped with 578,200 kN of thrust and pullback and 20,337 Nm of rotational torque, helping it penetrate through different and difficult terrains. Other features on the machine include an operator-controlled rod loader, climate-controlled cab, optional crane and optional front-mounted stakedown system.
The D60S has 266.9 kN of thrust and pullback and 12,202.4 Nm of rotational torque, helping it penetrate through different and difficult terrains. This power makes it one of the most powerful drills in its class. The additional features on the machine include a tethered remote control, ease of serviceability, three-speed gearbox, operator-controlled rod loader and climate-controlled cab.
Another enhancement made to both drills is the Plus+1 control system to maximise precision and reliability. Paired with the drill’s AutoSteer system, which automates certain drill head motions, it allows operators to set and adjust rotation duration and direction, while maintaining a pre-set thrust pressure to get through hard ground conditions. To top it off, the console design of the drill was updated to provide a user-friendly bore path adjustment experience for the operator.
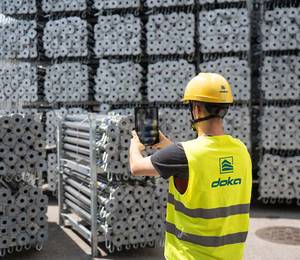
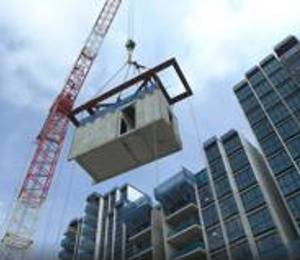
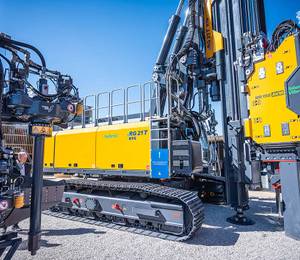
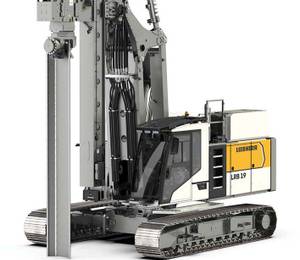
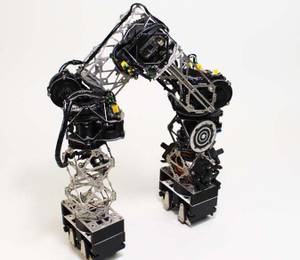
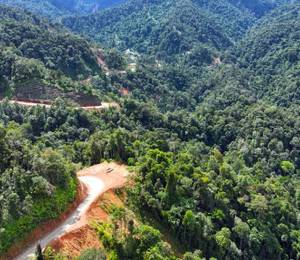
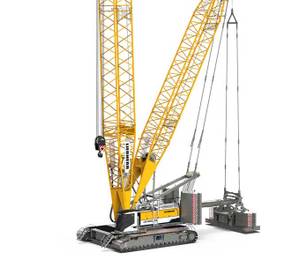