Bauer Maschinen GmbH offers a wide range of low-noise equipment - from drilling rigs to cutters - for use in foundation construction projects. “Reducing noise is an extremely important topic in the new development and ongoing development of our equipment,” said Christian Heinecker, head of business unit drilling equipment at Bauer Maschinen GmbH. “Thanks to our Energy Efficiency Package, EEP for short, Bauer equipment is now significantly quieter than the predecessor models without EEP.”
Bauer's smart eco mode relies on dynamic regulation of the engine speed based on the respective action being carried out. As a result, it not only reduces cumulative noise emissions but also reduces diesel consumption. This is assisted by an automatic motor stop function that automatically switches off the equipment if it is not used for a certain period of time. Optional add-on modules, such as inflatable noise control cladding for the power head or the upper carriage, also have a positive effect and can even be retrofitted to existing equipment.
The silent mode is used for Bauer equipment featuring standard technology without EEP. “This operating mode makes the new Bauer BG 15 H and BG 20 some of the quietest drilling rigs available in their class,” said Mr Heinecker. “The silent mode reduces the maximum engine speed and slows down the hydraulic consumers. Thus, the equipment’s noise level decreases by -2 dB(A).
“Compared with its predecessor model, the new BG 20 manages to reduce cumulative noise emissions by 9 dB(A). In some cases, individual measurements recorded values of just 100 dB(A). This is an extremely significant reduction in noise pollution, especially when we bear in mind that our perception of noise is not linear. A decrease of just 3 dB(A) means cutting the noise intensity in half, while a decrease of 6 dB(A) actually reduces the noise intensity by 75%!”
Drilling method matters
Apart from the equipment, the drilling method also influences noise emissions, highlighted Bauer. A differentiation is made between intermittent (e.g. Kelly drilling) and continuous methods (e.g. drilling with an auger using the displacement pile or double-head drilling method). “The latter method combines pulling and concreting into a single process, and for this reason produces lower emissions during excavation than a method such as Kelly drilling,” said Bauer. The company noted that, however, the continuous method is limited in terms of drilling depth and drilling diameter.
For Kelly drilling, Bauer's adaptive Kelly retraction assistant reduces the speed during the retraction process at the joints of the Kelly bar, which has a positive effect on the noise level generated. Various assistants help during drilling and discharge, for example by preventing the drilling tool from overfilling (over-drilling) and thereby facilitating the subsequent discharge process. The optimal filling level of the drilling tool is displayed for the operator in the B-tronic. During discharge, a one-directional or bi-directional spoil discharge assistant helps the operator. The one-directional spoil discharge assistant can be used to optimise the intensity when shaking out the auger.
Mr Heinecker pointed out, “Whether EEP, silent mode or assistance systems, many individual components result in a noise-optimised package at the end. We continually optimise our equipment and conduct our own foundation research as well as participating in publicly subsidised research projects.”
CBC silent cutters
Besides drilling rigs, noise reduction is also a priority for Bauer’s cutting technology. The EEP has been designed for the company’s cutter carrier machine, the MC duty-cycle cranes. The cutter itself produces low levels of noise and cutting is ultimately a low-vibration and thus low-noise method.
Bauer has further developed a compact series of cutters with low noise emissions, the CBC silent cutter. Two models are available - the CBC 30 for cutting depths of up to 80 m, and the CBC 45 for cutting depths of up to 120 m. The units feature a hydraulic power pack, which ensures silent operation.
The power pack is not permanently attached to the rear of the support frame as usual, but can be positioned on the side or even separately next to the support frame and connected via hydraulic lines. “This modular system, which is also available as a low headroom variant, offers maximum flexibility even in very tight spaces,” said Leonhard Weixler, head of business unit diaphragm wall technique at Bauer Maschinen GmbH.
The power pack is housed in a container with a length of 6 m, width of 2.5 m and height of 2.5 m. Compared with the standard MC duty-cycle crane from Bauer, the silent cutter produces noise emissions that are 3 dB(A) lower, which corresponds to approximately half of the perceived noise as described above. “That’s a major step,” said Mr Weixler. “This is possible because the separate power pack provides extra volume for noise insulation.”
The CBC silent cutters are ideal for use in urban environment projects, such as subway construction, where noise regulations can be very strict. “If the equipment needs to operate 24 hours a day in the city centre, it needs to be appropriately quiet. The factors here are official requirements, health requirements and, last but not least, economic considerations,” explained Mr Weixler.
Bauer’s silent cutters have also been introduced around the world. In 2014, the CBC 45 was deployed for foundation engineering work on subway shafts in the narrow urban canyons of Singapore. At the in-house exhibition in 2017, Bauer presented a CBC 30 compact cutter with low headroom configuration featuring a height of just 6 m; additionally, a CBC 30 is currently in production for future use in the US.
In 2018, Bauer handed over a CBC 45 to a long-established customer from Japan. And as part of the Grand Paris Express project, multiple compact CBC silent cutters have been used and continue to be used alongside numerous standard Bauer cutter systems consisting of a MC duty-cycle crane and BC cutter.
Images: Bauer Group

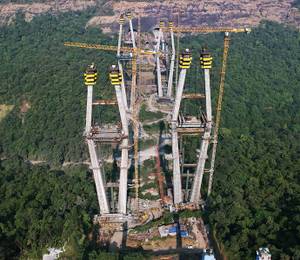
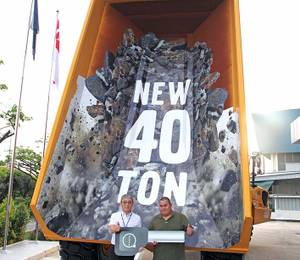
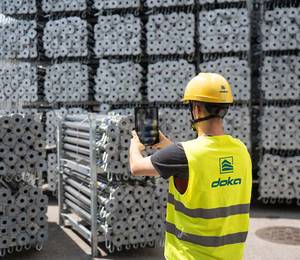
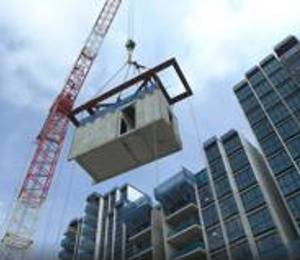
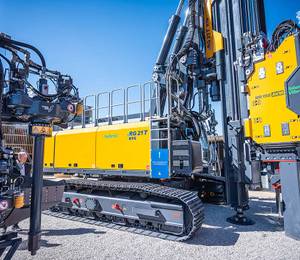
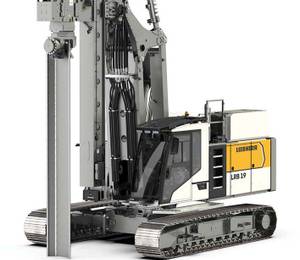