The new MB-HDS shafts screener from MB Crusher can be used in various applications to process a wide range of materials, such as excavation and demolition materials, asphalt, coal, organic materials, wood, bark and light plastics. The screener also enables the products to be re-purposed immediately.
“It is possible to transform one material into another effortlessly any time you need to: this is the most important and useful innovation,” said Diego Azzolin, production director at MB Crusher. “In fact, with the MB-HDS screening bucket you can easily change the rotating shafts on site in complete safety: just one person can do this in a matter of minutes. Our patented system keeps the rotating supports in place, the rotors can easily be removed and re-positioned, while the angular alignment is kept in place.”
“The new MB-HDS series is radically different from all the other systems available on the market,” continued Mr Azzolin. “It has been designed to be a real wild card: it can adapt to a range of different working environments and can select different types of materials with unprecedented simplicity and speed, without the need for a specialist or special training.”
The new MB-HDS screening bucket can be mounted on excavators, diggers, mini diggers and loaders - from 5 to 35 t – to perform works on construction sites and areas with large pipelines, towns or remote agricultural areas. There are four models available in the MB-HDS series, with shafts suitable for different material selection requirements. Changing of the rotary shafts can be carried out anywhere; they have a centralised greasing system and all maintenance tools are located inside a compartment of the shafts screener.
The MB-HDS series also takes care of the machine on which it is installed. An automated shock-absorbing hydraulic system reduces the discharge so that the engine, transmission components and the machine boom do not suffer any damage.
“Compact, reliable, sturdy and safe, the MB-HDS units are designed to be multi-purpose and highly versatile as well as being quieter to operate,” said Mr Azzolin. “It is possible for companies to use them in towns and historic centres, where there are different types of materials that need to be screened but both space and time are limited. The new system reduces noise levels by 40% when processing materials, in accordance with the regulations, thereby eliminating the need for exterior noise-control systems.”

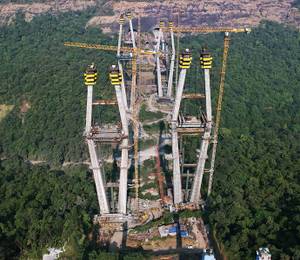
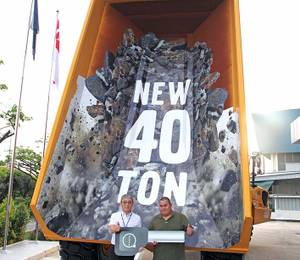
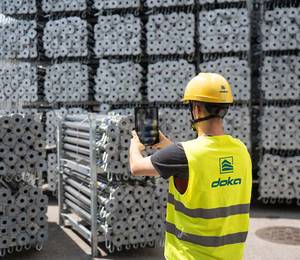
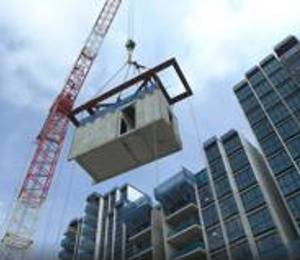
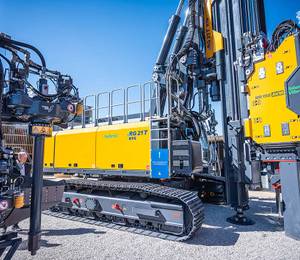
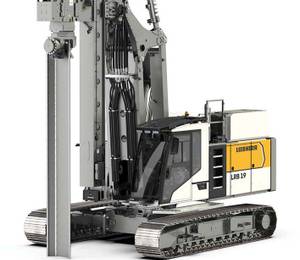