Ammann ARX 91 articulated tandem roller utilises high compaction output to make quick work of thick or thin asphalt layers in fewer passes. The output is provided through a combination of drum dimensions, frequencies and amplitudes. Applications include medium and large jobsites, including paving projects related to infrastructure, such as roads, airfields, harbours and parking lots.
The ARX 91 has a weight of 9 t, maximum working speed of 7 km/h, maximum travel speed of 12 km/h and gradeability of up to 40%. It is powered by a Cummins BS-III/Tier 3/Stage 3A engine. The machine’s propulsion system features an efficient hydraulic system, traction control and speed sensors. This enables smooth starts and stops that improve asphalt mat quality.
The location of the engine in the rear of the roller is another advantage. It helps drive vibration away from the operator and towards the compaction target. It also improves visibility and redirects heat from the operator, thereby increasing comfort.
The ARX 91’s electronic joystick controls are intuitive, making it easy for operators to use the machine. A tight turning radius improves operator control and manoeuvrability. A large water tank (1,000 l) minimises the need for refills.
Ammann Compaction Expert (ACE), Ammann’s proprietary Intelligent Compaction system, is available as an option on the ARX 91. ACE monitors density and provides feedback, helping to reduce the number of passes. It also eliminates both overcompaction and undercompaction and reduces fuel consumption.
In addition, Ammann ABC ValueTec asphalt-mixing plant is built to provide efficiency – and ultimately reduce costs and improve profits. It is suitable for business owners who want straightforward processes and the ability to further customise with options. According to Ammann, the plant offers the lowest product life cycle cost of all products in the segment and customisation enables the use of 25% to 40% recycled asphalt.
Key to the plant is the intuitive CS100 control system, which provides efficiency during production and also delivers built-in statistical reports to uncover cost-saving opportunities. A compact, modular four- or five-bin feeder ensures quick transport and assembly, and the plant’s small footprint allows it to fit into tight spaces.
The quality of mix from the ABC ValueTec can be made consistent from the feed stage, thanks to its large storage capacity. Frequency controlled conveyors extending to the drum inlet chute ensure hassle-free material delivery. The fully modulating burner features a simple, easy-to-adjust mechanism to set the air/fuel ratio for precise combustion and emissions control. The burner combines with the baghouse to ensure suspended particulate matter (SPM) levels are within limits and the carbon footprint is minimal.
The plant’s direct-coupled gear motors add value by reducing fuel and maintenance costs. Quality is boosted through a screen that uses vibratory motors, providing uniform distribution of aggregate on the screen mesh surface. Circular material movement and transverse transport between the two shafts ensure thorough mixing.
Ammann also offers the RSS 120-M, a mobile machine that prepares recycled asphalt for use in an asphalt plant. It is essentially a 3-in-1 machine that functions as a shredder, iron separator and screener. It is ideal for recycling asphalt that ranges in size from millings to larger pieces/slaps. The machine can go from installation to production in as quickly as 30 minutes, said Ammann.
A single operator can run the RSS 120-M, which is comprised of a shredder that utilises two low-speed, electrically driven shredder-rotating shafts. The machine features milling cutters with interchangeable teeth that crush the material. This technology significantly reduces the power requirement, which leads to substantial fuel savings. The technology also enables crushing of hard and soft materials, such as clays, and can perform in all types of weather.
The electric motors ensure consistent crushing and screening, regardless of the working environment. The RSS 120-M is able to process up to 180 t of recycling materials per hour. A variety of green efforts are built into the machine, including a dust reduction system and minimised sound and emission levels.

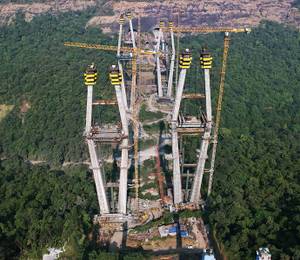
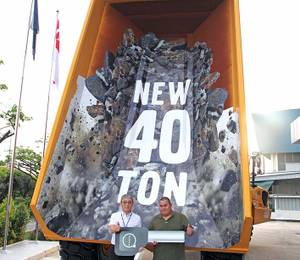
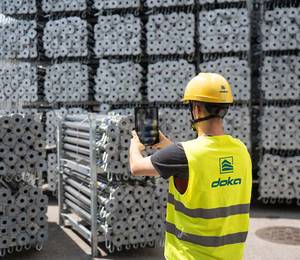
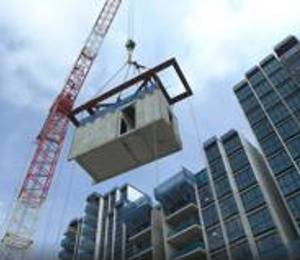
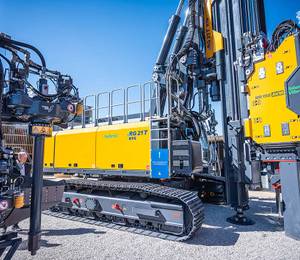
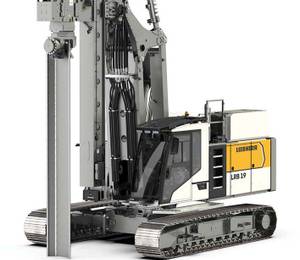