Precast building products have become an attractive choice for many projects in Asia and around the world, especially where productivity is highly required. Among the most practical innovations is Acotec, a non-load bearing precast partition wall panel that is designed for fast, simple and safe installation.
Developed by Finnish manufacturer Elematic, Acotec wall panel is made from either Leca (a lightweight expanded clay aggregate that contains natural materials) or concrete, thus ensuring great resistance against moisture and temperature differences while also dampening sounds from elsewhere in the building.
Acotec wall is ideal for residential buildings, public premises (such as hospitals, schools and service flats), warehouses, security fences and noise barriers. Practically, it can be used in any application anywhere in the world, said Elematic.
The length and thickness of Acotec wall can be adjusted on the production line in accordance with the application and construction requirements. The thicker the wall, the better its sound insulation and fire resistance properties. Elematic said it can even result in up to 120 minutes of fire resistance, depending on the thickness.
Due to its standardised shape and light structure, Acotec wall can be installed up to 90 sq m per day by two workers (simple wall), with the average being 50 sq m per day, according to Elematic. Building work can proceed up to six times faster when compared with traditional brickwork and about two times faster than blockwork.
Acotec wall also has exact dimensions and a completely even surface, so no plastering is needed. Elematic highlighted that despite its thinness, the wall is strong and has been used in seismic areas. It is also suitable for wet rooms such as bathrooms, kitchens and showers, thanks to the moisture resistance of the material.
The Acotec wall production line has three automation and capacity levels - Semi, Pro and Edge - to meet various customer needs. The Semi line, with a production capacity of 80 sq m per hour, is the simplest of all. It features a smart combined restacker handler and automation only for the key processes.
The Pro line has a higher capacity of 100 sq m per hour, with automated functions for all main processes: sawing, trimming, stacking, restacking, cleaning and oiling, plate handling and pallet circulation. The fully automatic Acotec Edge offers the highest capacity of 120 sq m per hour and needs only two operators to run.
Above: The Xuan Mai Sparks Tower in Hanoi, Vietnam, uses about 100,000 sq m of Acotec wall panels, with 100 mm thickness.
Entering Myanmar
Elematic has been involved in the development of modern precast technology across Asia for more than three decades - in countries like Singapore, Malaysia, Philippines, Thailand, Vietnam, Korea and India, among others. The company is now raising awareness of the benefits of precast technology in Myanmar, along with its partner Rieckermann, a Germany-based industrial solution provider.
Elematic has partnered with Rieckermann since 2013 in Myanmar, but precast technology is still considered new to the market “The country is lacking standardisation of the technology as well as experience in precast engineering,” said Ismo Kallio, vice president of sales at Elematic. “So people across the board – such as architects, planners and construction companies – all need to be made aware of what precast can really do.”
Traditionally, Myanmar’s construction industry has been site-based which has resulted in a lot of inefficiency – delays, cost increases, material wastage and even unsafe working practices. This is when precast solutions could be optimised for the use of more efficient and less costly construction, explained Stefan Bonin, general manager for Myanmar at Rieckermann.
As Myanmar is opening up its economy, the country plans to launch numerous residential projects to meet the housing needs in Yangon and other big cities. Precast technology is seen as a practical solution to help build these developments quickly, safely and cost effectively.
Above: Elematic and Rieckermann recently held a seminar in Yangon to raise awareness of precast technology and its benefits.
The Acotec wall panel is one of precast technology solutions that Elematic has introduced to Myanmar. The market is currently using the Semi production line, which is the simplest method that offers a production capacity of 80 sq m per hour.
“Due to rapid development of cities and their unregistered housing colonies, the need to create affordable housing for citizens is urgent,” said Mr Bonin. “Precast production in controlled factory conditions has huge potential to help Myanmar with its housing challenges.”
The proposal from the Myanmar government reportedly presents several challenges for developers. The plan is public–private partnership - based, where the land can be supplied by the state but building work is done by the construction companies.
“Because the projects require large investments from developers, they need to be completed on time and with minimal disruption. Using Elematic’s production technology is ideal for the whole construction of large housing blocks,” added Mr Bonin.
But it’s not just a question of cost - Myanmar’s position in an earthquake-prone region also creates challenges with construction of safe housing and making the right choices is even more essential. Elematic pointed out that through thorough research and testing, it has been determined that precast concrete can perform equivalent or even better to a cast-in-place structure in seismic conditions. “Precast methods are being deployed in many other highly seismic areas,” said Mr Bonin.
Precast is a greener choice too, thanks to the use of less raw materials. “Compared to cast-in-situ, the method uses less cement, less water and less steel. It produces less waste on-site and in factory, and the need to use expensive imported cement is lower as a result,” continued Mr Bonin.
It is still considered early days for precast in Myanmar and the technology awaits wide spread adoption, but the response from developers has been overwhelmingly positive, revealed Mr Kallio. “People are clearly interested in the use of precast and how it can help to create better, more sustainable buildings in less time and in a safer environment.”
Above: Elematic precast technology has also been involved in many building projects across India.
Website: www.elematic.com
Note: More detailed information on Elematic precast technology in Myanmar has also been published in the Sept/Oct 2018 issue of Southeast Asia Construction.

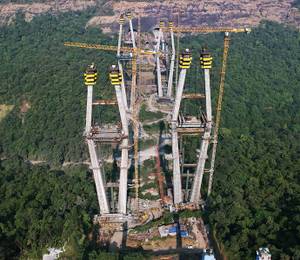
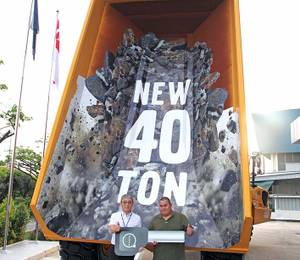
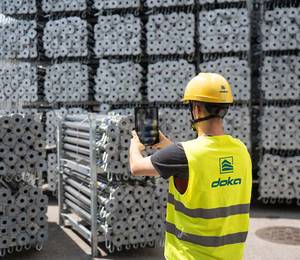
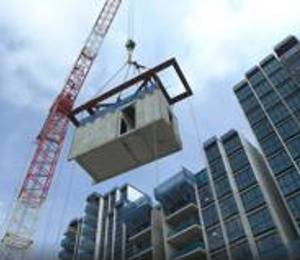
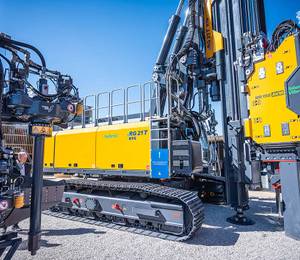
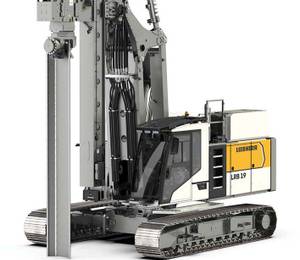